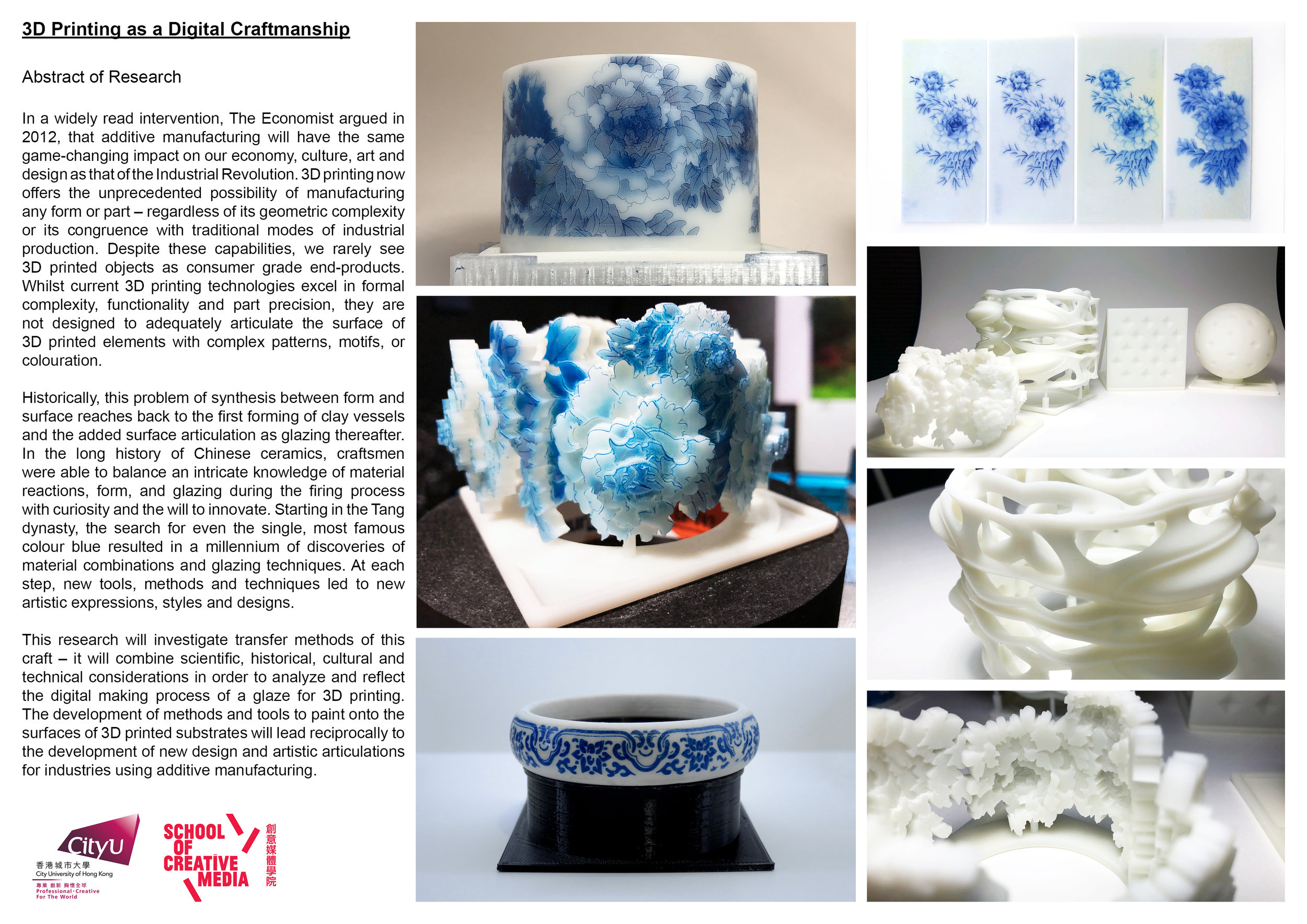
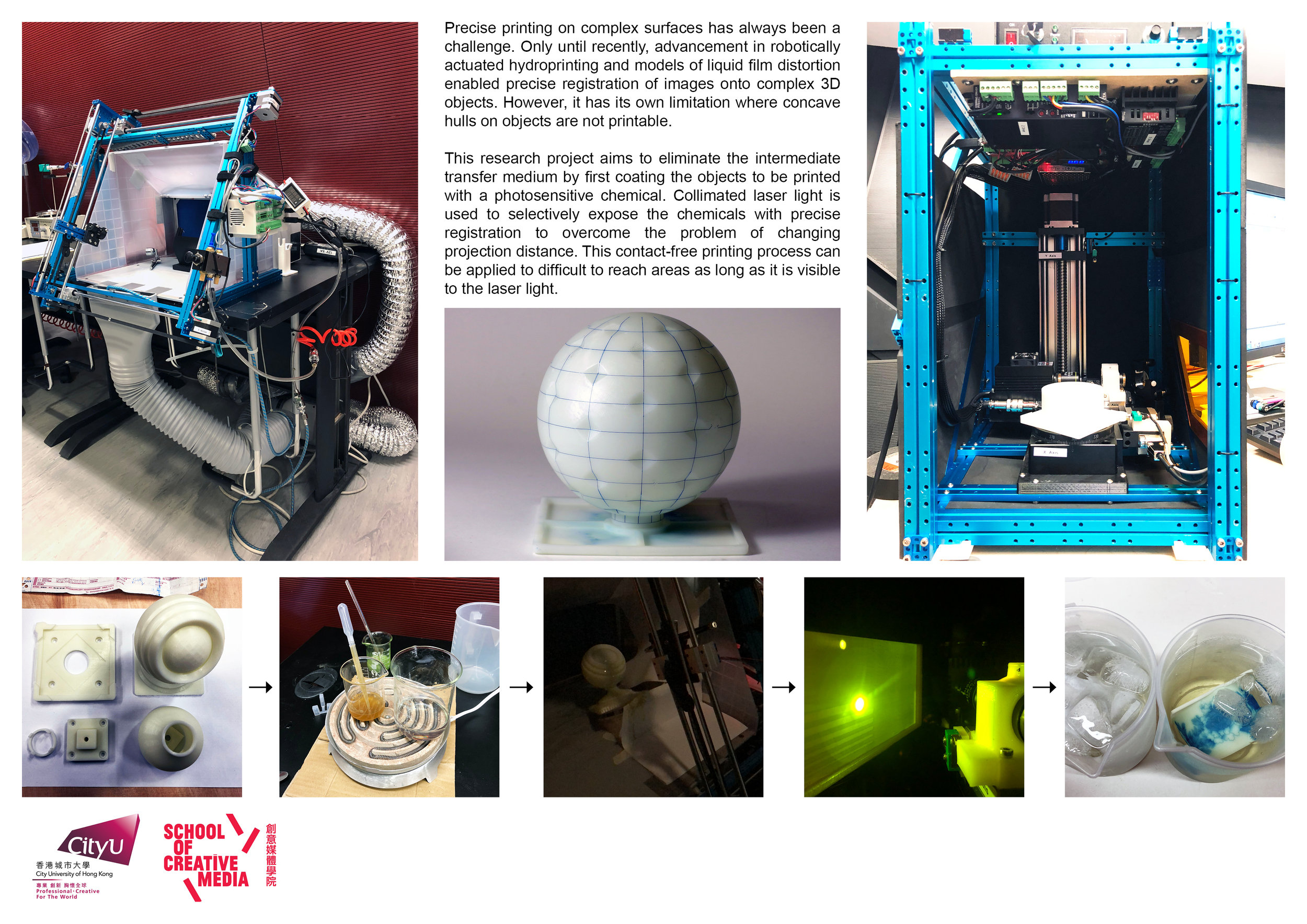
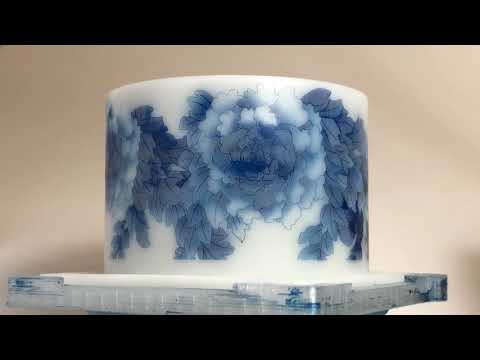
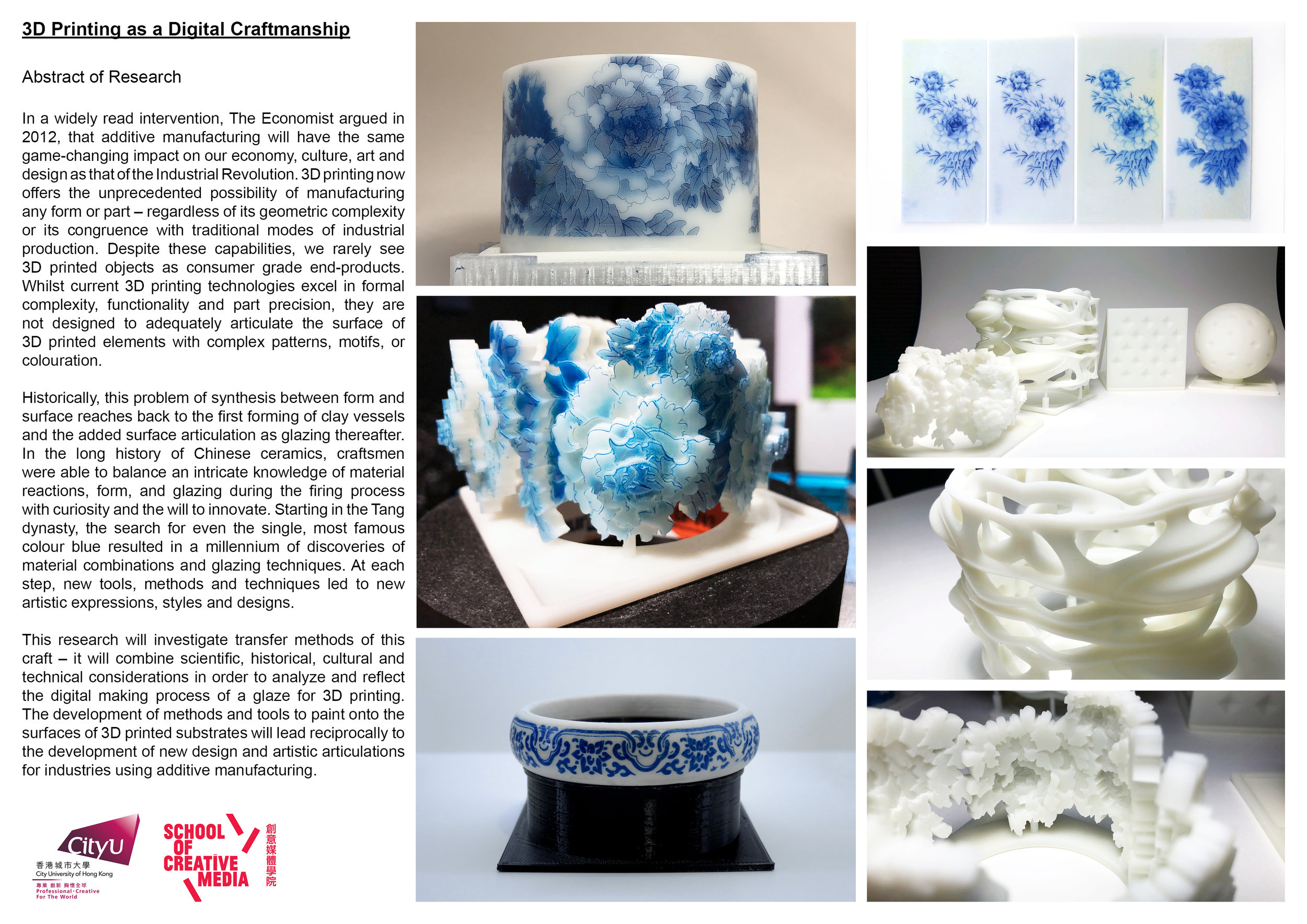
In a widely read intervention, The Economist argued in 2012, that additive manufacturing will have the same game-changing impact on our economy, culture, art and design as that of the Industrial Revolution. 3D printing now offers the unprecedented possibility of manufacturing any form or part – regardless of its geometric complexity or its congruence with traditional modes of industrial production. Despite these capabilities, we rarely see 3D printed objects as consumer grade end-products. Whilst current 3D printing technologies excel in formal complexity, functionality and part precision, they are not designed to adequately articulate the surface of 3D printed elements with complex patterns, motifs, or colouration.
Historically, this problem of synthesis between form and surface reaches back to the first forming of clay vessels and the added surface articulation as glazing thereafter. In the long history of Chinese ceramics, craftsmen were able to balance an intricate knowledge of material reactions, form, and glazing during the firing process with curiosity and the will to innovate. Starting in the Tang dynasty, the search for even the single, most famous colour blue resulted in a millennium of discoveries of material combinations and glazing techniques. At each step, new tools, methods and techniques led to new artistic expressions, styles and designs.
This research will investigate transfer methods of this craft – it will combine scientific, historical, cultural and technical considerations in order to analyze and reflect the digital making process of a glaze for 3D printing. The development of methods and tools to paint onto the surfaces of 3D printed substrates will lead reciprocally to the development of new design and artistic articulations for industries using additive manufacturing.
We propose a combination of material experiment, catalogue, design application and public dissemination, as an experimental, yet inclusive interdisciplinary research method. We will create an index of suitable chemical reagents and develop mechatronic and software tools for their application on 3D printed surfaces. We will test these new tools on the available 3D printed substrates, establishing design prototypes for digital craftsmanship.
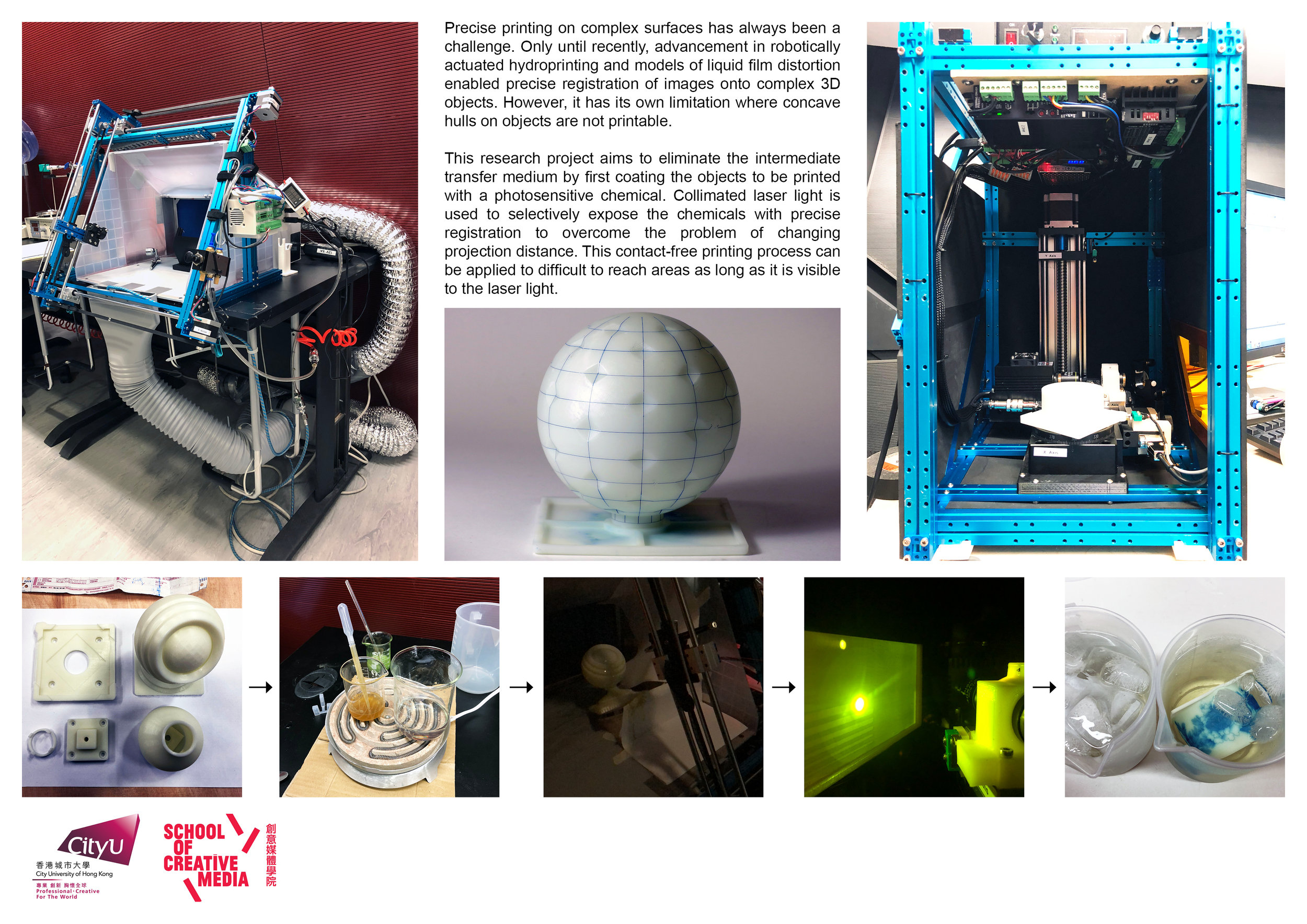
Precise printing on complex surfaces has always been a challenge. Only until recently, advancement in robotically actuated hydroprinting and models of liquid film distortion enabled precise registration of images onto complex 3D objects. However, it has its own limitation where concave hulls on objects are not printable.
This research project aims to eliminate the intermediate transfer medium by first coating the objects to be printed with a photosensitive chemical. Collimated laser light is used to selectively expose the chemicals with precise registration to overcome the problem of changing projection distance. This contact-free printing process can be applied to difficult to reach areas as long as it is visible to the laser light.